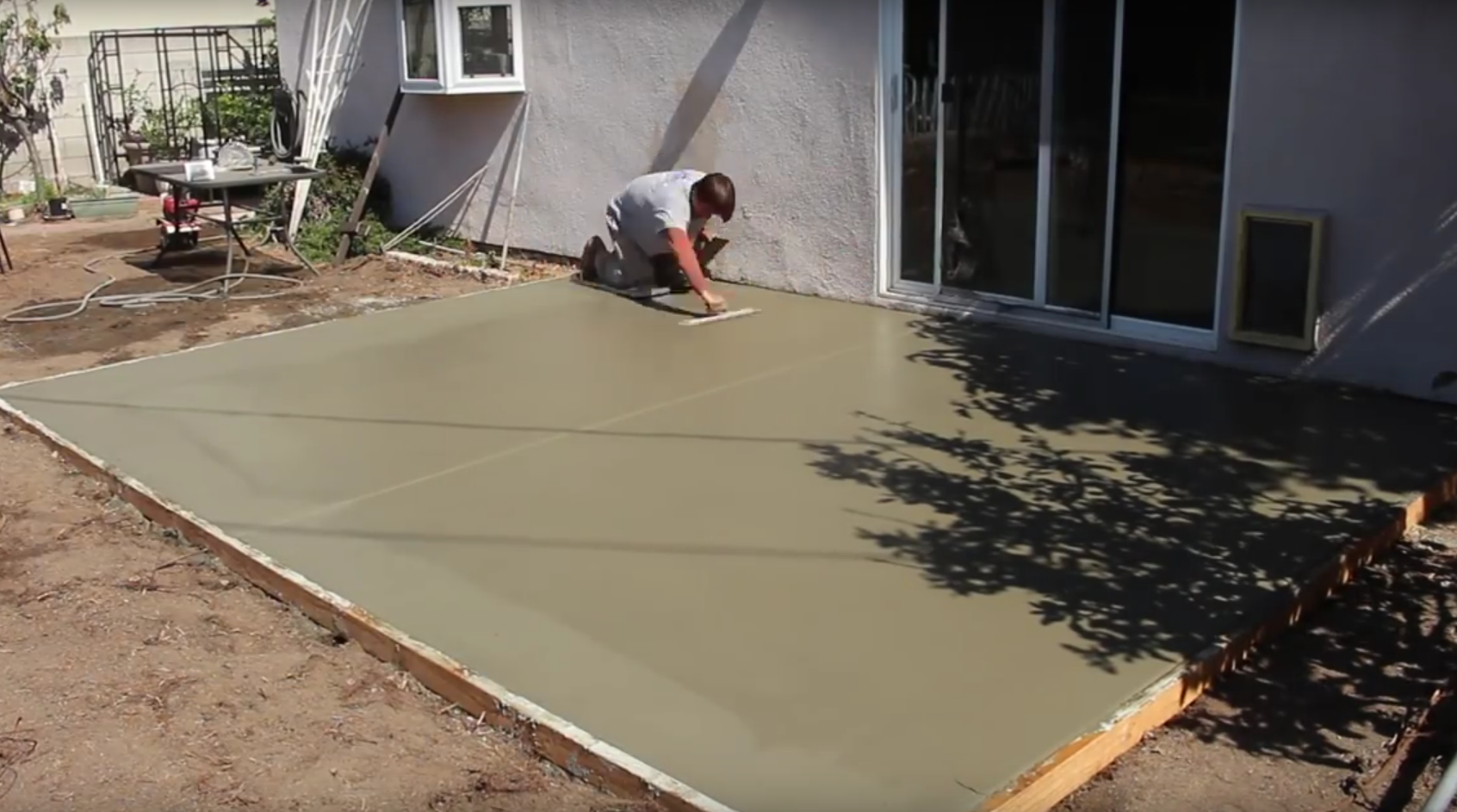
14 Mar Concrete Ideas
Working with concrete is something most of us will experience at one time or another when we work on our homes. It may be something as simple as a sidewalk or as complicated as footings for a foundation wall. But what exactly is “concrete”?
Table of Contents
Key Concrete Ingredients
Concrete contains three basic ingredients: cement, aggregate, and water. Cement, or Portland cement, is the glue that holds everything together; a fine, dry powder that solidifies and becomes quite strong when mixed with water. The majority of concrete is the aggregate. Aggregate is a mixture of clean sand and gravel. It must be clean for the cement to bind to it and it must contain enough fine material (sand and small gravel) to fill the spaces between the larger pieces of gravel. The final ingredient is water. The water combines with the cement in a chemical process called hydration. What this means is that the cement begins to form crystals between the pieces of aggregate, resulting in a strong, solid rock-like material. The key to good quality concrete is the right amount of water. Too much water will result in weak concrete. Most concrete mixtures are a ratio of 1 to 2, or 1 part water to 2 parts dry materials.
Additional Concrete Ingredients
Sometimes concrete contains other ingredients or admixtures. In cold climates, air entrainment is the most common. Air entrainment is a fancy way to say that there are microscopic air bubbles in the finished, hard concrete. These air bubbles help the concrete withstand the freezing and thawing that would otherwise ruin the surface of the concrete. There are other admixtures that are used for extremely hot weather, delaying finishing time or to prevent the concrete from freezing before it has a chance to cure.
Trying to figure out just how much concrete you will need can cause more headaches than any other part of concrete work. But with a few simple math tricks, it is quite easy. First of all, concrete is purchased in “yards”. This refers to the volume of concrete in cubic yards. To arrive at the number of yards you will need is to figure out the volume in cubic feet and divide by 27, which is the number of cubic feet per cubic yard.
If your project is a walk, patio or other slab type project, you first need to figure out the thickness of the slab in fractions of a foot. A 4-inch thick slab is the average thickness and is .33 feet thick (or 1/3.) Next, measure the length and the width of the slab for the total surface area. If you are pouring a patio that is 10 feet by 15 feet, your surface area is 10 x 15, or 150 square feet. Then multiply the square footage by the thickness of your slab to find the cubic footage (150 x .33, or 49.5 cubic feet.) Divide that by 27 to arrive at the cubic yardage (49.5/27, or 1.8 cubic yards.) Add another 5 % for waste and you come to 2 cubic yards of concrete for a slab that is 10 feet by 15 feet and 4 inches thick.
If your patio is round, its a bit trickier, but just as easy to figure once you have the formula. To find the surface area of a circle, find the radius, which is the length from the center of the circle to the edge (or half of the diameter.) Multiply the radius by itself and then multiply the answer by 3.14 (or pi.) Multiply this by the thickness of your slab and you have the cubic footage. For example, you have a circle that is 10 feet across. The radius is 5 feet. 5 x 5 is 25 and 25 x 3.14 gives you 78.5 square feet of surface area. Then multiply 78.5 by .33 and you get 25.9 cubic feet. To find the number of cubic yards, divide by 27 (25.9/27, or .9 cubic yards) with waste figured in, your patio should use about 1 yard of concrete.
If your project is an odd shape, just divide it into smaller shapes and figure the area of each shape separately. Then add everything up and multiply by the thickness to arrive at the total cubic feet and find the cubic yards as before. Remember that all your measurements must be in feet or fractions of a foot, not inches.
If you are pouring footings for a wall, the area is figured in the same way, except you first figure out the cross-section of the footing. A footing that is 6 inches high, 8 inches wide and 25 feet long would be figured in this way: 6 inches is .5 feet, while 8 inches is .66 feet. So, .5 x .66 is .33 square feet. Take this area and multiply by the length of your footing to arrive at the cubic feet. 25 x .33 comes to 8.25 cubic feet. Find the cubic yards by dividing by 27 and you come up with .5 cubic yard (8.25/27, or .3 cubic yards plus waste.)
While it may seem a daunting task to figure out how much concrete you will need, if you take it one step at a time, you should be able to figure it out in no time. Don’t forget to double check your math and it would be a good idea to have your measurements handy when you call in your order. Give the concrete salesperson the figures and have them work it out to be sure your math is right. That way, you will have enough to finish your project without having to pay for concrete you can’t use.
Before your concrete arrives, you need to have the site ready to pour. This means site preparation and setting up forms. This part of the concrete project should be finished at least the day before the concrete comes. You want to have everything ready for the arrival of the concrete.
Site Preparation
All site prep involves excavating of some sort. Footings need a trench, while slabs need to have enough soil removed from the sand or gravel base plus and concrete that will be below ground level.
To prevent the soil from settling under the concrete, it must be poured on undisturbed soil. If you dig too deep, you will either have to add more sand or gravel (packed down firm) or more concrete. In warmer areas with firm soil, where freezing is not a problem, the concrete can be poured directly on the prepared soil unless the building code calls for a sand or gravel base.
Forms
When pouring footings, setting up forms can be as easy as making sure the soil is stable. If it is, you can use the trench itself as a form. Otherwise, you will need to build forms to keep the concrete where you want it.
To support a wall, continuous footings need to be 6 to 12 inches thick. The forms are built from either 2×6 or 2×12 lumber. The forms for 6-inch footings are supported by stakes about every 3 feet, while 12-inch footings are staked every 2 feet. This helps support the forms so that the wet concrete does not push the forms out of shape.
The forms for a slab can be made from 2x4s with stakes every 4 feet. If you are pouring a large slab, such as a driveway, you will need to place expansion material every 10 feet or so to help prevent the slab from cracking when it expands and contracts with the weather.
Reinforcement
Concrete needs to be reinforced to help it support the weight placed on it and to help it survive the changes in the weather. Footing usually contains two steel reinforcing bars, or rebar, laid the length of the footing. When you need to use more that one piece to run the length of the footing, overlap the rebar by 15 to 20 inches (or what is called for in your local building code.) When placing rebar in the corners of footings, bend the rebar around the corner rather than having the rebar meet at the corner. This helps provide a strong, stable corner. Check with your local building code to see how much concrete must cover the rebar in footings. Usually, this is about 3 inches, which means that you need to support the rebar to keep it 3 inches below the top of your form.
Reinforcing a slab is usually reinforced with welded wire mesh. This mesh comes in 6 foot wide rolls and is cut with wire cutters. Reinforcing mesh in slabs usually needs to be about 1.5 inches below the surface.
Hiring a Pro
With all the work that is needed in prepping the site, building forms and reinforcing the concrete, I highly recommend hiring a professional concrete contractor to do the work. Small concrete jobs, such as a sidewalk, can be done without the help of a pro. Just make sure you feel comfortable doing the job yourself.
Screeding
The first thing you will want to do is screed the concrete as it is poured into the form. This is done by dragging a screed (nothing more than a straight 2×4) across the top of the form in a sawing motion. This will push the extra concrete along in front of the screed while showing you where the low spots are. Screeding only levels off the concrete, it does not smooth, or finish, the surface.
Floating the Surface
As soon as you have all the concrete in the form and it has been screeded, you want to float the surface of the concrete. A wood or metal float is used to push the aggregate into the concrete and flatten the surface. This is done by gliding the float back and forth over the concrete with the leading edge of the float slightly raised. A bull float is used to reach the center of large slabs.
Floating will not give you a smooth surface, but it will get the surface ready for smoothing. Once you are finished floating, you will notice that there is water sitting on the surface of the concrete. This is bleed water brought to the surface by floating. You need to wait till the bleed water has evaporated before you can move to the next step. This can take up to an hour or more, depending on the weather. If you have ever watched concrete pros finishing concrete, you will have seen them cleaning tools and sitting around drinking coffee. All of the sudden…it’s a mad rush to finish the concrete.
Finishing the Surface
You can leave the surface as it is after floating. On a slab, the marks left be the bull float will be straight across the surface, while a sidewalk that has been hand floated will have arcs left by the float.
You can drag a damp, stiff broom lightly over the surface of the concrete, creating fine lines running in the same direction. This is the best surface for sidewalks since it leaves a non-skid surface once the concrete dries.
After you screed the concrete, you can spread decorative aggregate over the surface of the concrete and then push them just below the surface with a float. Once the concrete sets, use a broom and a fine spray of water to go over the surface, washing away the top film of concrete and exposing the decorative aggregate.
Finally, you can produce a smooth surface by using a steel trowel. An expert with a steel trowel can give the finished concrete a surface that is almost as smooth as glass.
In Conclusion
Now that you know the basics of working with concrete, you are in a better position to decide if you want to tackle a concrete job as a do-it-yourself project, or if you want to hire a pro. Many times, you can help out with some of the work even though you hired a pro. There’s always wheelbarrows of concrete to move and tools to clean. Screeding is at least a three-man job on larger slabs. So talk it over with your pro…you may be able to make the job a partial do-it-yourself project.